As the user’s requirements for the safety and comfort of commercial vehicles continue to improve, auto parts factories have higher and higher quality requirements for commercial vehicle driveshaft forgings.
As an important part of the automobile transmission system, the driveshaft is used to connect the transmission and the drive axle to transfer torque and rotary motion. As the user’s safety and comfort requirements for commercial vehicles continue to improve, automotive parts factories for commercial vehicle driveshaft forgings quality requirements are also higher and higher. This paper focuses on the development trend of commercial vehicles, to analyze the impact of the market on the development of commercial vehicle driveshaft forgings quality, and how to improve the competitiveness of commercial vehicle driveshaft forgings in the market.
The main types of drive shaft forgings
Transmission shafts are divided into equal-speed drive shafts and non-equal-speed drive shafts, and non-equal-speed drive shafts are one of the key components of commercial vehicles. There are many types of drive shaft forgings, such as spline hubs, spline shafts, intermediate flanges, universal joint forks, sliding forks, spline shaft forks, end face flange forks, etc., see Figure 1.
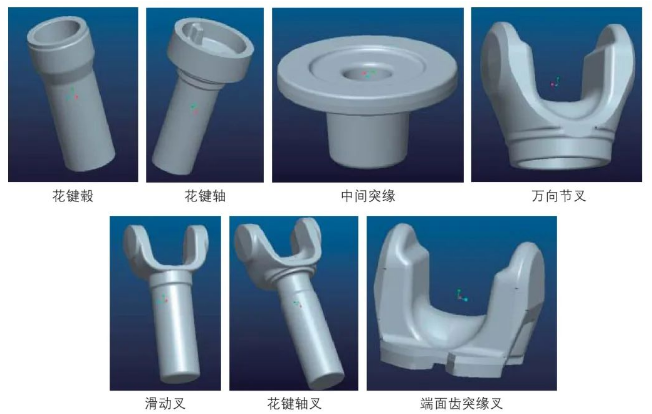
Figure 1 Main types of drive shaft forgings
Quality development trend of drive shaft forgings
- With the accelerated development of China’s logistics industry, the express delivery industry, which is mainly based on highway logistics, is demanding for “high speed” and “punctuality”, and the original users of commercial vehicles do not have high requirements for driving speed, but now they have increased the requirements for driving speed, which is very important for the manufacturers of commercial vehicle driveshafts. Commercial vehicle driveshaft manufacturers have to improve the driveshaft speed, torque on the efforts to increase speed requires forgings have a higher degree of symmetry, torque increases require forgings have a higher intrinsic quality. Part of the castings on the drive shaft is gradually replaced by forgings, which can also be fully explained on the mechanical properties of the drive shaft and the inherent quality of higher requirements.
- due to the highway load limit, commercial vehicle users in order to carry heavier goods, in exchange for higher profits, requiring a reduction in the vehicle’s own weight, most of the vehicle manufacturers are now launching a “lightweight” cars, such as: Shaanxi Automobile to promote the new Delong M3000, Delong X3000, etc., vehicle manufacturers are bound to require supporting enterprises to reduce the weight of parts, so as to reduce the weight of the whole vehicle, so as to achieve the goal of reducing the weight of parts. Reduce the weight of parts, so as to reduce the weight of the vehicle for the purpose.
With the progress and development of society, automobile users not only have higher requirements for the safety performance of the vehicle, but also improve the driving comfort requirements, such as: vehicle vibration, noise, cab comfort. In terms of commercial vehicle drive shafts, it is specifically reflected in: ① heavy series to reduce vibration, dynamic balance of the initial amount of unevenness from the original 300g-cm to the current 150g-cm; ② light series to reduce vibration, dynamic balance of the initial amount of unevenness from the original 50g-cm to the current 20g-cm.
With the improvement of drive shaft assembly standards, drive shaft forgings manufacturers must improve the quality of forgings as soon as possible, mainly in: consistency of forgings size, the amount of misalignment, curvature, deformation, surface defects and so on.
Transmission shaft forgings manufacturer what to do?
First of all, we must strengthen communication with customers, specifically to strengthen the contact with the customer’s technical department to achieve synchronous development of drive shaft components and forgings, so as to achieve the forgings in the material selection and structure tend to be reasonable (especially whether it is conducive to forging of the formation), and to meet the customer’s needs for fewer, no cutting, machining allowances, etc., and ultimately to achieve the optimal design of the forgings. Specifically manifested in the following aspects:
To “equal strength, lightweight” on the efforts.
A, mainly reflected in the communication with the customer’s technical department, optimize the structural design of the parts, remove redundant functions, reduce the weight of forgings, to achieve the goal of lightweight drive shaft parts.
B, on the existing parts of the material through the excellent instead of the poor, so that forgings (parts) in the strength and other mechanical properties of the same situation to achieve a substantial reduction in the weight of forgings (parts).
C, “hollow” forging requirements, on the one hand, without reducing the strength of the case, to achieve a reduction in the weight of the parts, such as: hollow spline shaft, hollow spline shaft fork; on the other hand, in order to save machining costs, as well as to achieve the purpose of saving raw materials, such as: hollow sliding fork.
D, the application of non-tempered steel in the drive shaft forgings, through the application of non-tempered steel to achieve the goal of energy saving and consumption reduction, there is no mature example in this field.
E, large modulus spline shaft (fork) cold rolling technology, large modulus spline sleeve cold extrusion molding technology and other advanced forging and molding process will further promote the drive shaft life is further enhanced.
F, part of the forgings using sub-temperature forging, hot and warm joint forging, warm and cold joint forging and other advanced forging technology, to achieve the utilization of forging materials, organizational structure, forging precision and appearance of the further enhancement of the quality, and make the die life can be significantly improved, energy consumption decreased significantly.
Improve the utilization rate of forging materials.
Domestic forging industry overall material utilization rate is not high, so high material utilization is the most critical part of the enterprise to enhance market competitiveness, then how to improve material utilization? The author believes that we should start from the following points.
A, according to the structural characteristics of the forgings, the use of less no fly forging, improve the material utilization of forgings.
B, the advantages and disadvantages of the forging process is the key to high and low material utilization, the advantages and disadvantages of the forging process is mainly reflected in the billet making process is reasonable, when the entire process design is completed, three-dimensional forging simulation can be used to verify that the current forging process is more reasonable through repeated verification to find.
From the rough forging to refine the forging aspects.
A, open die forging is reflected in the following aspects:
① Reduce the machining allowance: to ensure that the forging machining allowance is sufficient and minimum, forging size tolerance to precision level. Such as: according to the characteristics of the parts allowance from the original unilateral 2 ~ 3mm reduced to 0 ~ 1.5mm, significantly reducing the machining allowance, reducing the weight of forgings, to achieve the goal of energy saving.
② Control of oxide skin: residual oxide skin on the surface of the forging is too large, resulting in unevenness of the surface of the forging after shot blasting, the need to use less oxidation-free heating technology to reduce the generation of oxide skin, while in the process of production should be through the billet process and other means of removing oxidized skin in the production process to strengthen the education of workers’ sense of responsibility, so as to ensure that the forging of the aesthetics.
③ Control knock injury: reduce forging processes in the high temperature billet, forging knock, need to take corresponding measures to solve the problem. Such as: through the elimination of molds and discharging channel of the sharp corners, to reduce the high temperature billet and forging bump.
④ Reduce the residual burr: the current labor costs are getting higher and higher, grinding burr process is to increase the cost of forging process, such as to reduce the number of grinding burr, reduce the cost of forgings, the need to think of ways to cut the edge of the process from the hot cutting, mainly in the development of different products in the different cutting temperature range, and matching the corresponding hot cutting edge die, in the forging process in a timely manner to replace the cutting edge of the die with the mold to match the die.
B, occlusion forging: according to the characteristics of the product as far as possible using occlusion forging, in order to further improve the material utilization of forgings.
Die life improvement:
Improve die life is also the top priority to reduce production costs, improve die life can be used in the following ways: ① mold application of new materials; according to different process characteristics of different materials, using different heat treatment hardness; ② mold surfacing technology application; ③ mold surface strengthening technology can make the mold life to achieve the effect of doubling the effect of improvement; ④ selection of high-quality environmentally friendly demolding lubricants and other technical means.
Here is our partner factory to take countermeasures
(1) The forging process adopts Deform auxiliary design, and the application advantages are as follows:
A, new product development: Deform software can simulate the entire forging production process of new products, through numerical simulation can determine the forging process and molds, simulation through the computer, reducing the number of times of trial molds, saving the new product development cycle and cost.
B. Optimization of forging process: Through Deform simulation, the existing forging process can be analyzed to find out the problems in the forging process. The simulation output contains the flow direction of metal, temperature distribution and stress distribution, etc., which makes the whole forging process more intuitive and easy to understand.
C, forging mold design and correction: CAD software through the design of the mold after the three-dimensional modeling, can be in the Deform software forging simulation, so as to find out the problems that exist in the forging mold, and make corrections to it.
D, forging blank design: through the Deform software simulation of the entire forging process, you can determine the specifications of the forging blank (optimal diameter and length) and weight, maximize material utilization.
E, forging defects analysis: the analysis of the forging results output by Deform, you can find out the folding, lack of meat, size overruns and other defects in the forging, and make corrections to them.
(2) The use of 3D measurement technology.
A, 3D scanning can be used to detect the key dimensions of complex forgings (no way to measure manually), bending, misalignment, machining positioning datum changes and other aspects, see Figure 2.
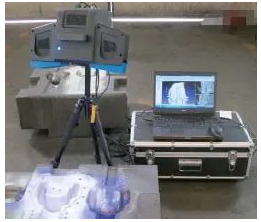
Fig. 2 Picture of on-site measurement of molds
B, the measurement of complex molds:
① can use the theoretical mold cavity and the actual scanning of the mold cavity comparison, to check whether the new mold is qualified, to reduce unnecessary losses due to unqualified dimensions, see Figure 3.
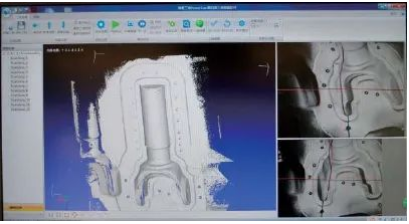
Figure 3 Scanning to generate three-dimensional model picture
② detection of changes in the mold during the forging process, the accumulation of data in the design of the mold will be prone to wear and deformation of the parts to give a reasonable compensation to improve the service life of the mold.
(3)The mold management process improving, see Figure 4.
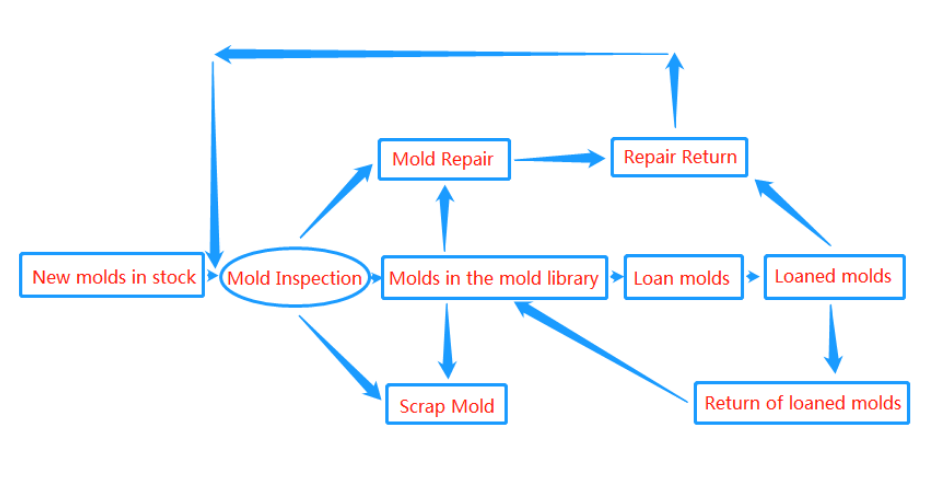
Figure 4 Flow chart of mold management
A set of die has only one ID code for life, which can reflect the different failure modes of a set of die at different stages in the process of completing its mission, and the establishment of a database facilitates the optimization of die structure design and ensures the consistency of forging quality.
Conclusion
With the rapid development of the automotive industry, parts manufacturers must further improve product quality to meet the requirements of users and automobile manufacturers, which forces parts manufacturers must be “innovative” to re-examine their own products, otherwise they will be defeated by competitors, eliminated by competitors out of the game.